Radio Frequency Identification (RFID) and Manufacturing Execution System (MES) software help streamline and optimize the production process in a carpentry factory. Van de Vin windows and frames in Heeze (NL) also experience this. MarixWindows application Manager Rudolph den Boer explains how RFID and MES contribute to a significant reduction in lead time. With the so-called VinTracking system, you can follow a window or door from A to Z, with many advantages.
Source: Carpentry Magazine 'Timmerfabrikant' (NL)
Text and photos: Kees de Vries
RFID
RFID is a technology to store and read information from a distance from so-called RFID tags on or in objects. These tags can actively or semi-actively reveal their data via a reader. RFID has recently been introduced in the wood carpentry sector, as is now the case with Van de Vin Windows & Doors in Heeze (NL). Rudolph den Boer, responsible for process control and automation, says: "The production of windows & doors is precisely customized with much research. It is traditionally associated with A0 sheets with frame views details. All in all, that's a whole pack of paper per project. Paper is practical but also very inflexible. Changes are always challenging to implement and take much time. Digitizing with RFID means that a windows & doors runs through our production in a better way and that every production step has the necessary information at hand. Our biggest goal at all times is lead time reduction. That is at the top."
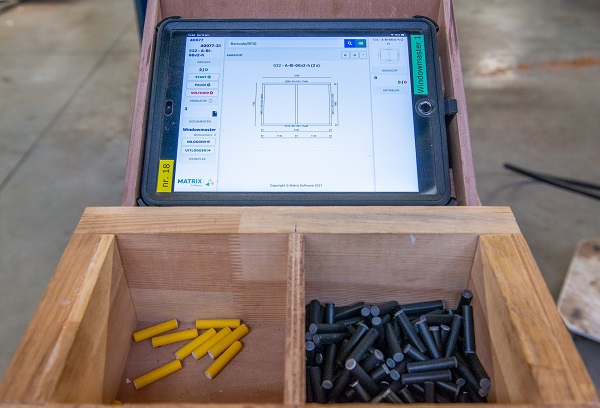
RFID and wood are not 'friends'. RFIDdirect developed an RFID tag for the wood sector that can be read well despite the wood moisture.
Identification via MES
Van de Vin and several similar companies started working with Matrix Software to link the Matrix window frame software and the Matrix ERP system to each other and make them accessible via screens and tablets in the factory. Van de Vin also studied techniques to identify every frame, window, and door during production. Den Boer: "Before the paint shop, each frame part can be easily identified with a barcode sticker. After that, it gets more difficult. We used to engrave the frame in our processing line, with which we could manually look up the frame on paper or PDF. But that's cumbersome. RFID makes it possible to quickly identify a frame, window, or door, from the machine department, via pre-assembly, spraying line, and final assembly. RFIDdirect helped us with that, and Matrix made it possible to have all relevant information directly available on a screen."

Application Manager Rudolph den Boer.
Datastream
The English company RFIDdirect is a so-called 'solution provider' that, with 25 years of experience, develops innovative RFID solutions for stock tracking and project management in the wood processing industry. The company can supply both hardware and software, and it is a specialist in passive tags that are suitable for reading up close with a reading device. No lines of sight are required, as with a barcode. Van de Vin uses UHF RFID technology. The tags remain inactive until the reader 'wakes them up' and operate on Ultra High Frequency (UHF), a short-carrying frequency range of 865 MHz to 928 MHz. From an office just across the border in Kleve, Germany, RFIDdirect closely follows developments in the wood sector. Business development manager Auto-ID Mohssine Ouchen says: "The market is going to robotize. This involves a huge data flow. Van de Vin and many of their colleagues are increasingly discovering the benefits of RFID."
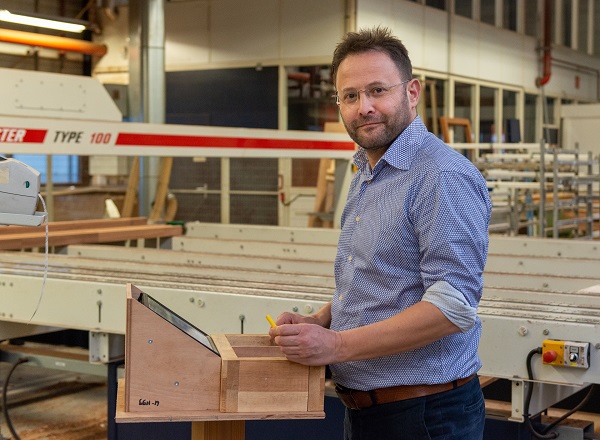
Mohssine Ouchen, Business Development Manager Auto-ID at RFIDdirect.
No friends
Due to the moisture present, RFID and wood are not friends. Therefore, the standard tag is a problematic medium to read quickly and without interference. RFIDdirect has developed a special plastic dowel-shaped tag especially for the wood sector that is invisible after the first processing with an additional 50 mm deep drill hole of 8 mm but always attached to a fixed location in the frame connection (in the bottom left corner of the frame). "It is also important that the tag can be read all around and that it retains its function up to the 75-year lifespan of the frame, window, or door. And we succeeded", said Mohssine Ouchen. "After-sales service and warranty can also be followed via this technique."
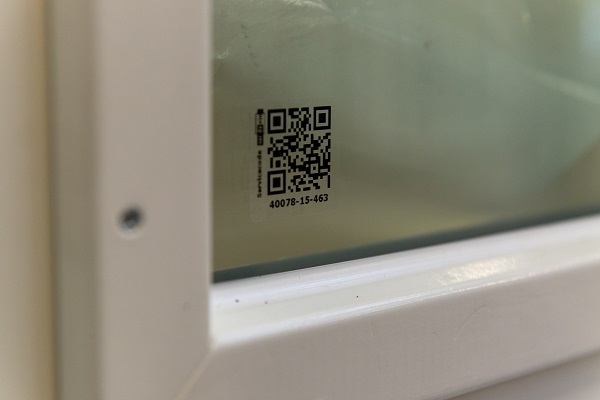
As a service, Van de Vin places a QR code on the glazed frame for the contractor with information such as project number, phasing, and the frame brand. That information also comes from the RFID system.
A lot of information
Van de Vin invested in the MES (Manufacturing Execution System) software platform from Matrix Software. Den Boer: "Each department is provided with the information required for the relevant production step, including associated details and specifications. Each work in the production ultimately receives information via a tablet needed for that specific production station. The RFID is inserted and 'loaded' after the first processing of the wood. This provides clarity and saves a lot of time and research. And the system is 'live.' So if I add a change in the work preparation, change frame sizes, change hinges and locks, or whatever, the system implements it immediately. A change also during the production process is immediately live so that everyone always has the same project information. Feedback from production has become much more efficient in this way. As soon as the desired adjustment has been processed, any follow-up phases that have already been prepared are immediately adjusted! The 'game' of work preparation, feedback, and production has become a lot more fun in this way. You automatically collect a new kind of data because you scan every frame, window, or door and follow it. This amount of data gives you much better insight into where improvements may be needed to get the most out of your production. The system is also good support for your subsequent calculation."

The RFID tag is inserted into the wood in a plastic dowel.
Materials passport
After completing the current step, Van de Vin also wants to equip its approximately 900 frame frames with an RFID tag to ensure exit control via Matrix MES and speed up the expedition. For the delivery note, only the buck needs to be scanned. Den Boer: "The costs of RFID are an investment, but if we can produce completely paperless in the future, we will almost break even. If you then add the time savings because there is no longer a need to search for information, this process ultimately yields money. Search work is pure waste. The ultimate wish is to include our service technicians in the tablet and reader system so that they have access to all data on the construction site, such as wood type, finish, hinges and locks." Den Boer continues: "As an intermediate step, we now stick a QR code on the glazed frame for the contractor with information such as project number, phasing, and the frame brand. Make important specific information accessible for each frame in the future, such as a materials passport, technical product information, and processing instructions. Van de Vin has now been working with the system for eight months."
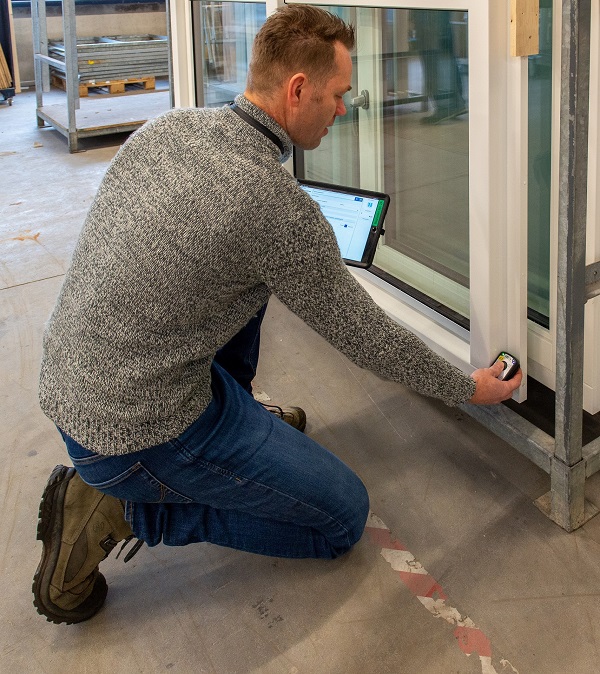
The RFID tag can be read with a reader and always has a fixed location, the bottom left corner of the frame.
Business Development Manager Mohssine Ouchen says: "A real pitfall in successfully implementing an RFID process is that the client/user wants too much and too quickly. The possibilities of this technique are vast, and each step certainly comes with its price tag in terms of hardware. RFIDdirect invests much time in personal guidance and process analysis to get the best result from the process." Den Boer: "It is custom work. It must fit into your company and work process. We started with a low-threshold and small-scale per workplace. Guiding the staff in the new working method is also important. We want to be completely paperless in a year." Interest in technology in the wood sector is growing. For the coming period, RFIDdirect has several agreements with other carpentry factories.